Lubrication Systems Servicing and Repairs
It is important that regular inspections and maintenance are carried out to ensure efficient operation of all equipment. Through careful planning and management we can assist in achieving improved operational times through the reduction of unplanned stoppages as a result of poorly serviced equipment.
Benefits of Regular Maintenance
Down Time
Scheduling maintenance for equipment can occur when the machines are at their lowest use or when not in use. The machines can be examined for wear and lubricants can be applied. Planning maintenance has several benefits. The machines are less likely to break when in use. If a machine stops working while in production, production is stopped until it is fixed. Employees can’t be productive and often must receive overtime after the equipment is fixed. Work falls behind. This can cause customer services issues if you have an order for a certain number of products, but you can’t deliver because the machine broke down.
Costs
Equipment or facilities that have regularly scheduled maintenance can save money. For example, if a maintenance person thoroughly looks at a building structure every three months, he can identify problems before they get worse and subsequently more expensive.
Preventative maintenance cost very little, but not attending issues is potentially much more expensive in time and parts.
Safety
Preventative maintenance can stop some safety issues that might occur.
Quality
Preventative maintenance can improve quality of products produced or services provided as it will reduces rejection of inferior product or services.
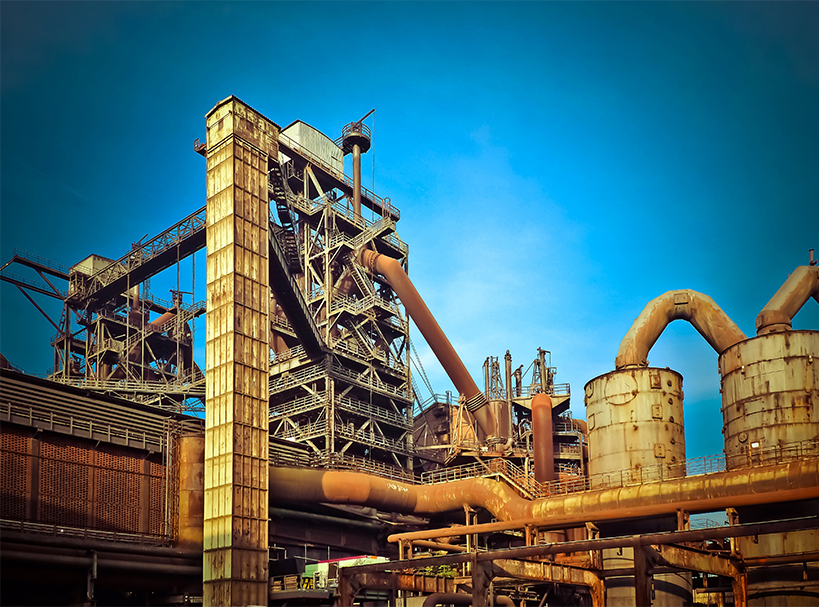